|
Project in progress - an LCD meter, using PIC's.
This
ongoing project uses an EPROM technology PIC, the 12C672, as an eight bit
analogue to digital converter, it has up to four analogue inputs, but this
design currently uses only two of them.
I've
got a couple of different schemes in mind with this project, firstly using
just the 12C672 (the gold coloured UV erasable chip on the right of the
first picture) to feed into a PC serial port, allowing data logging and
plotting of graphs etc. I've written the software in the 12C672 so it can
feed directly to a PC serial port, so it could make a very simple low
cost device. The battery discharge curves on my Misc pages were plotted in a
similar way, using an old hardware A2D connected to the PC parallel port.
Secondly,
as in the picture, using a 16C84 to feed an LCD display module, the 16C84
accepts the serial data from the 12C672 and displays it on the LCD - you
could use this to simultaneously display upto four different readings, for
example in a dual channel power supply, showing voltage and current for
both channels.
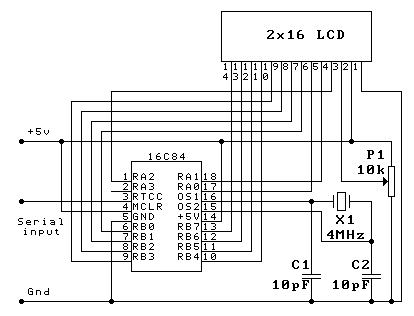 |
This
is the circuit of the display board, as you can see it uses very few
components, just the LCD module itself, a PIC16C84, a 4MHz crystal and
associated capacitors, and a potentiometer - used for setting the
display contrast. The RTCC (RA4) pin is used to input the serial data,
RA3 is the only pin left free. Not shown on this circuit is an
electrolytic capacitor I fitted across the supply rails, although
PIC's seem to work well without them I usually hang one across - in
this case it was a small tantalum capacitor that I had to hand - it
can be seen in the first photo below, just to the right of the 16C84.
If you feed the serial input via a 22K resistor, you could connect
this directly to an RS232 line, and monitor the data on the line.
The
display is fed in 8 bit mode, to use 4 bit mode pins 6, 7, 8, and 9 of
the display should be disconnected from the PIC and connected to
ground, this would free an extra four I/O pins, and I may well rewrite
the software to take account of that. |
The
analogue to digital board is even simpler, the 12C672 has an in-built
4MHz oscillator, avoiding the need for those components, so it
consists almost solely of the PIC - the two presets are only for
testing, providing varying voltages for the two channels. The TL341 is
a 2.5V precision voltage reference, used as the reference voltage for
the A2D converter in the chip, this gives a stable reference voltage,
and avoids errors due to supply voltage changes. R1 provides the
required current for the voltage reference, and give roughly 1mA
through the device. As the TL341 gives a 2.5V reference, I've added R2
and R3 to form a potential divider to bring the range back to 5V - by
changing the values you could read any voltage, but below 2.5V FSD
would require amplifying first. |
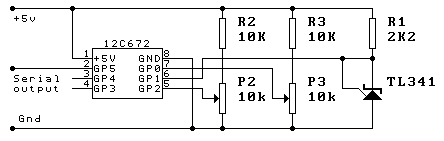 |
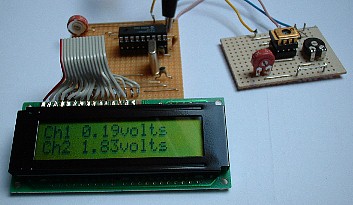 |
The
two boards connected together, the right hand board is the 12C672, the
two presets are for adjusting the input voltages for test purposes. |
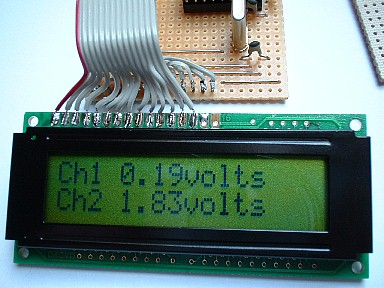 |
A
closer shot of the display, it's currently running in 8 bit mode,
which leaves 2 I/O pins unused, one is used for the serial input from
the 12C672, and the other is spare - I may use it to switch the
display to HEX mode, showing the Hexadecimal values of the incoming
data, I've already got the required routines written in the chip, I
used them during testing. |
The
software in the 12C672 reads the first input (AD0) and then multiples the
result by 195 to scale the 0-255 result to 0-50000, the resulting
value is then converted into a decimal string, with the lowest two digits
discarded. The decimal numbers are next converted to their ASCII codes, a
decimal point added, and the data sent out as standard 9600baud serial data,
cursor positioning commands are also added to the data stream, and the
various text additions as seen in the pictures. Once AD0 has finished, the
same is done for AD2, and the program then loops back to the start to give
continuous updates.
The
16C84 reads the data stream, and displays the incoming data, the cursor
positioning commands are striped out and processed separately - command and
display functions are driven separately on these LCD modules. In order to
detect command data, I first send a non-printing character (in this case
0x80) followed by the required data byte - the 16C84 detects the 0x80 and
jumps to a command routine which send the following byte to the display as a
command.
I'll
be adding the software listings once I've decided exactly what I want to do,
I'm open to any suggestions?.
|